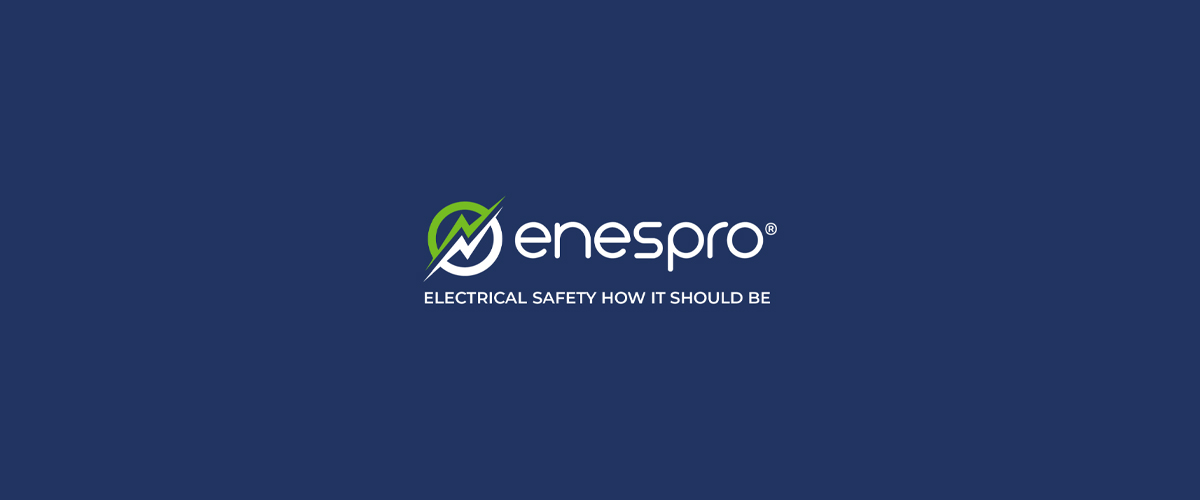
Common Scenarios That Lead to Arc Flash Incidents
Arc flash incidents are a serious hazard in workplaces that involve electrical systems. They can happen in an instant, causing severe injuries, equipment damage, and costly downtime. Despite strict safety regulations, arc flash incidents continue to occur due to common workplace issues. Occurring 5-10 times per day in the United States and resulting in over 400 fatalities and 30,000 incidents a year, arc flash occurrences are common, dangerous, and often deadly incidents. Understanding these scenarios is crucial for improving safety and protecting workers.
This article explores the leading causes of arc flash incidents and provides practical solutions to help organizations reduce risks. By the end, you'll have a clearer picture of how to enhance electrical safety and how innovative PPE solutions can support these efforts.
What Is an Arc Flash and Why Is It Dangerous?
An arc flash is a sudden release of electrical energy that occurs when an electrical fault causes current to travel through the air between conductors. This results in extreme heat, light, and pressure that can lead to severe burns, hearing damage, and even death. According to the Occupational Safety and Health Administration (OSHA), arc flash temperatures can reach up to 35,000°F—four times hotter than the surface of the sun—igniting clothing, melting skin, and causing life-threatening injuries in an instant. A line-to-line or line-to-ground arcing fault can escalate into a three-phase fault in less than 1/1000 of a second, leaving little to no time for reaction. The consequences can be devastating, from severe burns—often due to clothing ignition—to blindness, hearing loss, and permanent disabilities. In many cases, injured workers never fully regain their previous quality of life.
Why Do Arc Flash Incidents Happen?
While human error or carelessness of a worker account for the majority of incidents, arc flash can be the result of a wide variety of causes—static electricity, loose connections, or even a rodent in the vicinity that compromises the distance between energized components. Each of these factors presents unique challenges, but understanding them in detail allows organizations to take proactive measures to prevent incidents before they happen.
1. Human Error and Improper Procedures
No matter how well trained a worker is, accidents happen and are often the result of operator error. Distractions, weariness, pressure to get the job done quickly, or simply overconfidence can cause a worker to move too fast, fail to don personal protective equipment (PPE), or bypass other safety procedures. It’s estimated that two out of every three arc flash incidents occur as a result of human error and carelessness.
Often is the case, a worker will complete the same task many times over the course of a year, a decade, or a career without incident, developing bad habits while trying to save time. It only takes one mistake to cause the electrical current to become uncontrolled, even something as routine as a control panel adjustment could end up with deadly consequences.
Common mistakes that lead to arc flash incidents include:
• Failure to De-Energize Equipment Properly: Workers sometimes assume that equipment is safe to handle without verifying its de-energized state. Skipping essential steps in the lockout/tagout (LOTO) process can result in unexpected exposure to live circuits.
• Lack of Situational Awareness: Distractions, rushing, or working under pressure can lead to unsafe actions, such as inadvertently touching live components or bypassing safety controls.
• Ignoring Warning Labels and Procedures: Electrical equipment often carries warning labels that indicate the level of hazard. Workers who bypass these warnings or fail to wear proper PPE expose themselves to unnecessary risks.
• Overconfidence and Complacency: Experienced workers who have performed the same tasks for years may develop a false sense of security, leading them to take shortcuts or overlook critical safety steps.
2. Equipment Failure
Electrical equipment naturally degrades over time, and without proper maintenance, it becomes a major hazard. As insulation weakens and connections loosen, the likelihood of an electrical fault increases. Older systems, in particular, often lack the protective features found in modern electrical equipment, making them more vulnerable to failure.
Several factors contribute to equipment-related arc flash incidents:
• Aging Infrastructure: Many industrial facilities and commercial buildings rely on electrical systems that were installed decades ago. As components age, their ability to handle electrical loads safely diminishes, leading to unexpected failures.
• Lack of Predictive Maintenance: Reactive maintenance approaches, like fixing equipment only after it fails, can leave dangerous faults unnoticed. Predictive maintenance strategies, such as infrared thermography and electrical testing, can detect early signs of wear before they escalate into hazards.
• Improper Repairs or Modifications: Using substandard replacement parts or performing quick fixes that don’t meet safety standards can create hidden risks within the system. Temporary repairs can eventually lead to major breakdowns, increasing the chance of an arc flash.
• Corrosion and Contamination: Exposure to moisture, chemicals, and environmental pollutants can corrode electrical components, weakening their insulation and increasing the risk of electrical faults.
3. Incorrect PPE Usage or Lack of Compliance
Personal protective equipment (PPE) is the last line of defense against arc flash hazards, but it can only provide protection when used correctly. Unfortunately, many workers either wear the wrong PPE or choose not to wear it at all, putting themselves at significant risk.
Key issues related to PPE misuse include:
• Wearing Improper PPE for the Job: Not all PPE is rated for arc flash protection. Workers may unknowingly wear garments that do not meet the necessary arc rating for the electrical hazard they are facing.
• Discomfort and Non-Compliance: Some PPE can be bulky, hot, or restrictive, leading workers to remove it or wear it improperly. This issue highlights the importance of selecting lightweight and comfortable PPE that does not hinder productivity.
• Failure to Inspect PPE Regularly: Arc-rated clothing and equipment, such as gloves and face shields, must be inspected for wear and damage. Tears, burns, or worn-out materials can compromise the protective capabilities of PPE.
• Lack of Proper Fit: Ill-fitting PPE can leave gaps in protection or restrict movement, increasing the likelihood of accidents. Properly fitted gear is essential for ensuring full coverage and mobility.
Minimizing Risk of Injuries from Arc Flash
When deenergizing equipment isn’t an option, minimizing arc flash risk relies on following safety standards from OSHA, NFPA, and others. Key practices include lockout/tagout, approach boundaries, and proper labeling to reduce injury risk. Just as crucial is ensuring workers are trained, retrained, and equipped with effective, compliant PPE—critical steps in any arc flash risk mitigation strategy.
How Enespro Can Help Mitigate Arc Flash Risks
At Enespro, we understand the challenges that come with protecting workers from arc flash hazards. Our line of arc flash PPE is designed with worker comfort and safety in mind.
• Lightweight and Comfortable Designs: We prioritize comfort without sacrificing protection. Our PPE is designed to be lightweight and breathable, making it easier for workers to wear throughout their shifts.
• Enhanced Protection and Usability: Our products are engineered using innovative materials that offer superior protection against arc flash hazards while providing excellent visibility and durability.
• Compliance with Safety Standards: All Enespro PPE meets or exceeds NFPA 70E and OSHA requirements, ensuring that workers stay compliant while remaining protected in hazardous environments.
Arc flash incidents are preventable with the right combination of proper equipment maintenance, worker training, and high-quality PPE. By understanding the common scenarios that lead to these events, organizations can take proactive steps to protect their workforce.

Stay in the loop.
Sign up for our emails to be the first to know about exclusive product offerings
and all things Enespro.